Walking into the Crockett & Jones factory, you can smell the history – literally. Dating back to the 1890s, the walls of the Perry Street institution are imbued with the centuries-old scent of calf skin and resin, wax polish and wood. It’s a heady concoction on first whiff, like sniffing glue in the back of a Bentley.
Outside the Grade II-listed red brick building on a whisper-quiet residential street in Northampton, you’d have no idea of the scale and the skill of the work being executed inside.
To call it a ‘small factory’ would be disrespectful to the 300 employees inside; ‘large workshop’ is a more accurate description. For starters, there is no automation at any stage. And every one of those workers are artisans in their particular area: from cutters to closers, cobblers to welt stitchers, they are all craftspeople. There’s even one lady who spends her entire day gimping – the art of trimming and simultaneously decorating the edges of leather. I think that makes her a professional gimper.
FAMILY VALUES
In 1879, Charles Jones and his brother-in-law started the company with a £200 grant. Fast forward nearly 140 years, and Crockett & Jones now stands strong as the oldest family-owned and family-run shoemaker in the UK. This is quite some feat. The Brits essentially invented shoemaking as we know it – certainly the Goodyear-welted process – and this company is one of the oldest and arguably the very best in the entire trade.
It’s not exactly been a walk in the park, though. The company nearly went out of business in the 1970s. It was two weeks from going bust, and the sales director even paid the salaries from his private purse.
But they turned it around. And now it’s a genuine success story, a beacon for Great British handmade craft. Crockett & Jones now makes 120,000 shoes a year. It would make more – there’s certainly the demand for them – but the factory is at capacity.
There are 80 Crockett & Jones doors in Tokyo alone. Japan is hugely influential in global shoe fashions. Unlike some traditional shoemakers, Crockett & Jones is open to these trends. Of course, it will always make a black oxford and a brown brogue. But as demands change, it adapts and evolves.
For example, its latest collection – The Black Editions – fuses traditional styles with modern oversized, cleated soles made from lightweight rubber. From the catwalks of Milan and the sidewalks of Tokyo to the back streets of Northampton.
The Historic Crockett & Jones
STEP BY STEP
It’s difficult to appreciate just how complicated shoemaking actually is until you’ve witnessed it first hand. (Or should that be first foot?) For each pair of shoes produced there are more than 200 individual operations that take place across eight main departments.
First, is Pattern Cutting. The pattern cutters produce patterns for the last (the wooden form on which the shoes are made).
A prototype is made, tested, adjusted and then a final sample pair is produced. There are a lot of different parts that make up the whole. Take a wing cap shoe, for example. Each one is made up of nine different leather sections (including the lining). Multiply that by a pair, then by 16 size options, and that’s 352 different patterns for just one style of shoe. Crockett & Jones currently produces more than 400 styles. You do the maths.
When every check has been completed, the shoes enter production. The Clicking department kicks us off: here the shoe uppers and linings are cut. The name comes from the satisfying ‘click’ the knife makes as it is removed from the leather. A significant proportion of the final product cost comes from the leather. Crockett & Jones sources the best from three-four month-old calves. This is when the material is at its most supple and fresh with the tightest of fibres.
The company only uses the byproduct of veal, which explains why the majority of the calves are from France, Germany and Switzerland. More exotic materials are available – such as horse (cordovan) and crocodile. But the one thing that links them is that only the best are selected. Any imperfections, from flea bites to barbed-wire scratches, are not accepted.
Watching the craftsmen undertake these processes without any guide beyond years of practice and instinct is hypnotic
Next up is Closing. This term seems somewhat premature given its proximity to the opening of operations, but what it actually refers to is ‘closing’ the uppers. This includes everything from punching holes for brogues to fitting eyelets for laces.
Preparation follows – again, the name is misleading until given context: the preparation refers to the bottom part of the shoes. Soles are cut using heavy presses; insoles are prepared; heels are built.
The Lasting process is where the shoes start to take shape as the upper is pulled over the last before being side and toe lasted. In the basement, there are 40,000 pairs of lasts including ones that date back to the very start of the company. The rows upon rows of wooden racks are an impressive sight akin to the cellars of great wine chateaux.
The creation process in pictures
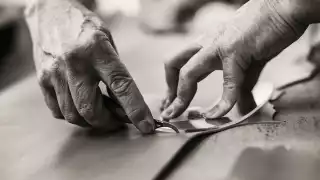
Clicking
The Clicking department kicks us off: here the shoe uppers and linings are cut. The name comes from the satisfying ‘click’ the knife makes as it is removed from the leather.
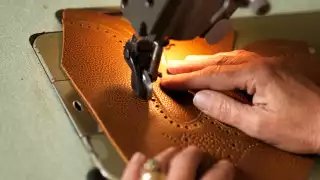
Closing
This term seems somewhat premature given its proximity to the opening of operations, but what it actually refers to is ‘closing’ the uppers. This includes everything from punching holes for brogues to fitting eyelets for laces.
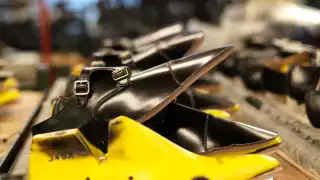
Preparation
The preparation refers to the bottom part of the shoes. Soles are cut using heavy presses; insoles are prepared (see above); heels are built.
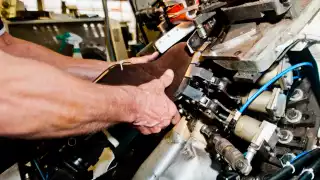
Lasting
The Lasting process is where the shoes start to take shape as the upper is pulled over the last before being side and toe lasted. In the basement, there are 40,000 pairs of lasts including ones that date back to the very start of the company.
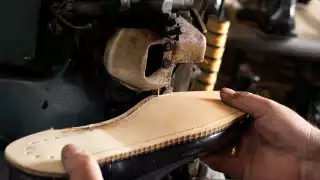
Making
The Making process includes ‘welt sewing’: stitching the welt (a strip of leather) to the rib on the insoles.
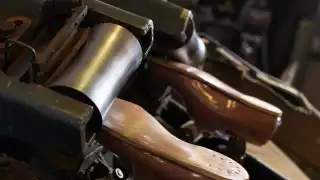
Finishing
Finishing is, again somewhat ironically, the penultimate department. Here is where the heels are attached, trimmed and scoured for a smooth finish.
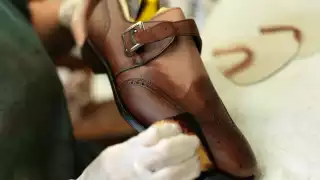
Shoe Room
The final department is simply known as the Shoe Room. Here the uppers are hand polished, often many times, using different techniques depending on the required effect.
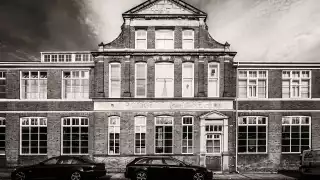
Where the magic happens
The Crockett & Jones factory in Northampton.
The Making process includes ‘welt sewing’: stitching the welt (a strip of leather) to the rib on the insoles. This welt is crucial to the renowned Goodyear-welted process, which also involves filling the bottoms of the shoes with cork and wooden shanks before stitching the soles to the welt. The method allows for the soles to be removed for repair without affecting the uppers. (The in-house cobbler, Gary, has been at the factory for more than 30 years. He pulls the shoes apart with the speed of a butcher and the dexterity of a surgeon.)
Finishing is, again somewhat ironically, the penultimate department. Here is where the heels are attached, trimmed and scoured for a smooth finish. Edge trimming is a highly skilled and physical process whereby the sole edges are trimmed to the specific shape of the last. Charlie, the edge trimmer, has been with the factory since he was 16. He’s 65 next year.
Perhaps most impressive of all is that every pair of shoes is worked on by almost every member of staff
What’s so astonishing about this, like most of the operations in Goodyear-welted shoemaking, is that it’s carried out freehand. Watching the craftsmen undertake these processes without any guide beyond years of practice and instinct is hypnotic. The speed is mind boggling; you half expect them to stitch the shoes to their hands.
The final department is simply known as the Shoe Room. Here the uppers are hand polished, often many times, using different techniques depending on the required effect.
The lasts are removed from the shoes, the leather soles are stamped with the Crockett & Jones brand, and the insocks are fitted. Only then will the final product be passed through an exacting quality control process. Nothing short of perfection is allowed inside those forest-green cardboard boxes.
What’s perhaps most impressive of all is that every pair of shoes is worked on by almost every member of staff. It’s like an orchestra – each person is an expert at their specific instrument, and each plays their part. On their own, they’re incomplete, but bring it all together and the result is symphonic. It may sound a bit lofty to compare making shoes to making music, but there’s no doubt these shoes have soul.
AW18 Collection
For more info, see crockettandjones.com