It’s 7am on a cloudy November’s morning when I clamber down the ladder of my waterfront pavilion and plunge into the frozen gloom of Lake Neuchâtel. Hotel Palafitte is the only hotel in Europe built on stilts and a chilling dip in the icy waters on which it stands is said to stimulate the mind and body. I last about 15 seconds, just enough time for the shock to wear off, before I’ve had quite enough stimuli thank you very much and race into the warm embrace of a hot shower. If this is indeed a daily ritual for the residents of Neuchâtel, then they are far braver than I. Then again, they build them tough in these here parts, as the watch manufacture sat on the hill overlooking the mediaeval town confirms.
Opened in 2014, the Manufacture Officine Panerai is the beating heart of the famed Italian-Swiss watchmaker’s operations. Featuring 250 specialists spread across 10,000 sq m of space, the modern building is responsible for the vast majority of Panerai’s fabrication processes, from case creation and movement assembly, to R&D and testing.
Walking through the clinical white production facility, the deafening whir of CNC machines shaping metals into innumerable components ringing in my ears, I spare a thought for Giovanni Panerai, the founding father of this storied brand, who opened his first shop in 1860 at Ponte alle Grazie in Florence. We’ve come a heck of a long way from that small boutique and workshop.
The Panerai name rose to wider prominence in the 1940s after Giuseppe Panerai was commissioned to produce a high-strength dive watch for the Italian Royal Navy. The watchmaker had been working with the Navy since 1935 on the development of various technical tools for military activity, including a timepiece, but it was the creation of the Ref. 3646 – the watch we now know as the Radiomir – where be began to see the modern guise of Panerai take shape.
Panerai’s big ideas are handled by a team of whizz kids collectively known as the Lab-ID
In many ways, this historic timepiece will sound all-too familiar: a cushion-shaped case, luminescent numerals and indexes, four large Arabic numerals at 12/3/6/9, and a sandwich dial that utilises overlapping discs to improve legibility. Much has changed in the world of horology, not least at Panerai, but one of the very first and most enduring dive watch designs continues to stand the test of time. The Radiomir is an integral part of Panerai’s offering to this day, alongside the Luminor, Submersible and Luminor Due collections.
My tour guide throughout my visit to the manufacture is Panerai’s chief operating officer, Jérôme Cavadini, who has worked at the brand since 2010, first as the director of manufacture and as COO since 2018. There are few better qualified to explain the strengths of the brand than my companion for the day.
“As watchmakers, we need to ask ourselves what does Panerai stand for? To me, it’s very clear what it stands for: tool watches for tough conditions. Everything that we are doing goes in that direction. In order to achieve this, we are pushing on different aspects, whether that’s movements or materials, but it always returns to this purpose,” Cavadini tells me.
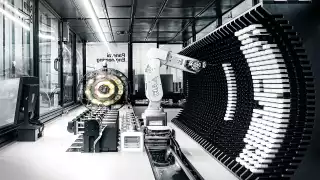
Mattia Aquila
And, yet, this ethos is nothing new for the watchmaker. The name Radiomir itself dates back to a Panerai patent filed in France on 23 March 1916, relating to a radium-based powder, which gave a vastly improved level of luminosity on the dials of sighting instruments and devices. The same powder was used for the hands and indices of the Ref. 3646. I should note that radium is a highly radioactive substance and that Giuseppe Panerai would later patent ‘Luminor’ in 1949, a tritium-based luminescent substance, which featured very low emissions that were totally harmless to the wearer. Like Radiomir before it, Luminor would become the identifier for another of Panerai’s watch collections.
Back in the present, Panerai’s big ideas are handled by a team of 20 whizz-kid project managers and contractors, collectively known as the Laboratorio di Idee (or, Lab-ID for short), who boast a wide range of expertise from the fields of watchmaking, engineering and even chemistry. “We are constantly looking for the next thing and the Lab-ID programme allows us to push the boundaries in certain directions to link with our DNA, whether that’s reliability, sustainability, shocks, luminosity – I don’t want to disclose everything that we are working on, but you will see in the next few years,” Cavadini says.
For a brand of Panerai’s size, it seems quite surprising that such a select group of individuals are responsible for much of the brand’s advancement. But while it might seem small, the results are mighty impressive: Panerai launched its first in-house movement as recently as 2005 when it released the P.2002, a hand-wound calibre with a GMT complication and a whopping eight-day power reserve. There are now 28 in-house movements in all, including high complications like a perpetual calendar, which took eight years of development for the Lab-ID team to perfect alongside Panerai’s head watchmakers.
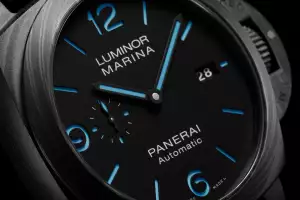
Mattia Aquila
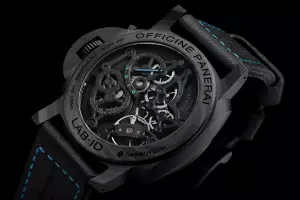
Mattia Aquila
The lengthy power reserve has become something of a signature, as well pushing industry standards upwards, as Cavadini explains: “We were certainly on the forefront of longer power reserves because we had our eight and ten-day calibres for quite a long time already. But, today, with the exception of one movement, our minimum power reserve is 72 hours and we plan to push that even further in the future.”
Outside of the movement, Panerai’s greatest contribution to the wider watchmaking conversation has been its forward-thinking approach to material innovation. Whether it’s Carbotech, a carbon fibre-based proprietary material that is uniquely lighter and less corrosive than both titanium and ceramic, or DMLS (Direct Metal Laser Sintering), the process of 3D printing cases using a high-powered laser and titanium powder, the watchmaker continues to push the boundaries of what’s possible from its watch materials.
“When it comes to creating tough tool watches, the first place to start is the case, so we are constantly looking for materials that can provide additional benefits to our watches. We don’t want material innovation just for aesthetics purposes. I don’t want to compare too much with other brands, but you can see that there are some using materials that are very nice to look at, but you can doubt whether it’s really fit for watch usage.
“We have a checklist of characteristics we are looking for from a material: it needs to be light, it needs to be tough or at least some scratch resistance, magnetic resistance – I mean, to name every characteristic is not that easy, actually. Then ideally it would bring a new aesthetic, but this comes, I would say, last in the list of priorities when we look for metal,” Cavadini says.
In this horological torture chamber, timepieces are subjected to a range of watch-breaking tests
“Over the past ten years, there are not that many brands which have launched as many new metals as Panerai – titanium, ceramica, Carbotech, DMLS, BMG. And this will continue to be at the heart of our operation. You will see next year something that is again, quite innovative, very interesting in terms of properties, in terms of mechanical properties, aesthetics. I mean, we are really touching every dimension of what we’re looking for when you look for new materials.”
So, how does it work? One can only assume that such groundbreaking materials don’t grow on trees. You won’t be surprised to hear that it is a lengthy and often challenging task, as Cavadini illustrates: “In terms of the process, a few of our Lab-ID project managers spend as much as half of their time going to universities to fairs to different types of industrial contacts to discover the latest material innovations. Sometimes, we’ll take things that already exist but have been developed for other purposes, and sometimes we’ll develop a material from the early stages.”
If a part of you had hoped that the laboratory part of Lab-ID was quite literal, I’m afraid that this isn’t the case: “You never develop a material entirely from scratch. These metals are not something that we can just take off the shelf, machine and then sell. It takes a lot of time and development, but this is how you push boundaries.”
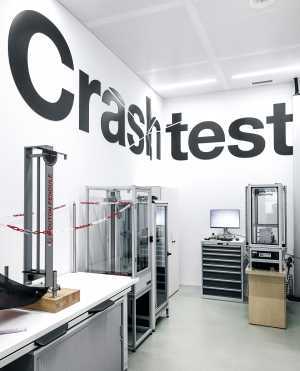
Mattia Aquila
Cavadini walks me downstairs to the ground floor and a quiet corner at the back of the production facility where the words “CRASH TEST” are emblazoned on the wall in large bold lettering.
It’s one thing to set out with the intention of building tool watches for the most extreme conditions, but it’s another thing entirely to subject your watch line-up to a rigorous quality control and testing process in order to guarantee the highest standards imaginable.
In this horological version of a torture chamber, timepieces are subjected to a broad range of watch-breaking tests, including climate tests, shock tests (roughly 500G of force delivered to a timepiece in an array of positions), the free-fall test (that imparts 3,200G of strain through a watch as it is dropped from a height), and accelerated ageing tests where the mechanism is wound and unwound thousands of times.
There’s also rate tests for movement accuracy, magnetism and water resistance tests, and corrosion tests for the case material. You can almost hear the sound of countless watches screaming under the strain.
“What I think is interesting at Panerai is that we have some very nice high-complication watches that are also very robust pieces,” Cavadini says, as we spy a Luminor Perpetual Calendar being put through its paces. “If you take our perpetual calendar or minute repeater, we test them as we would test anything else. When we do homologation on a prototype, they go through the same shock and drop tests.”
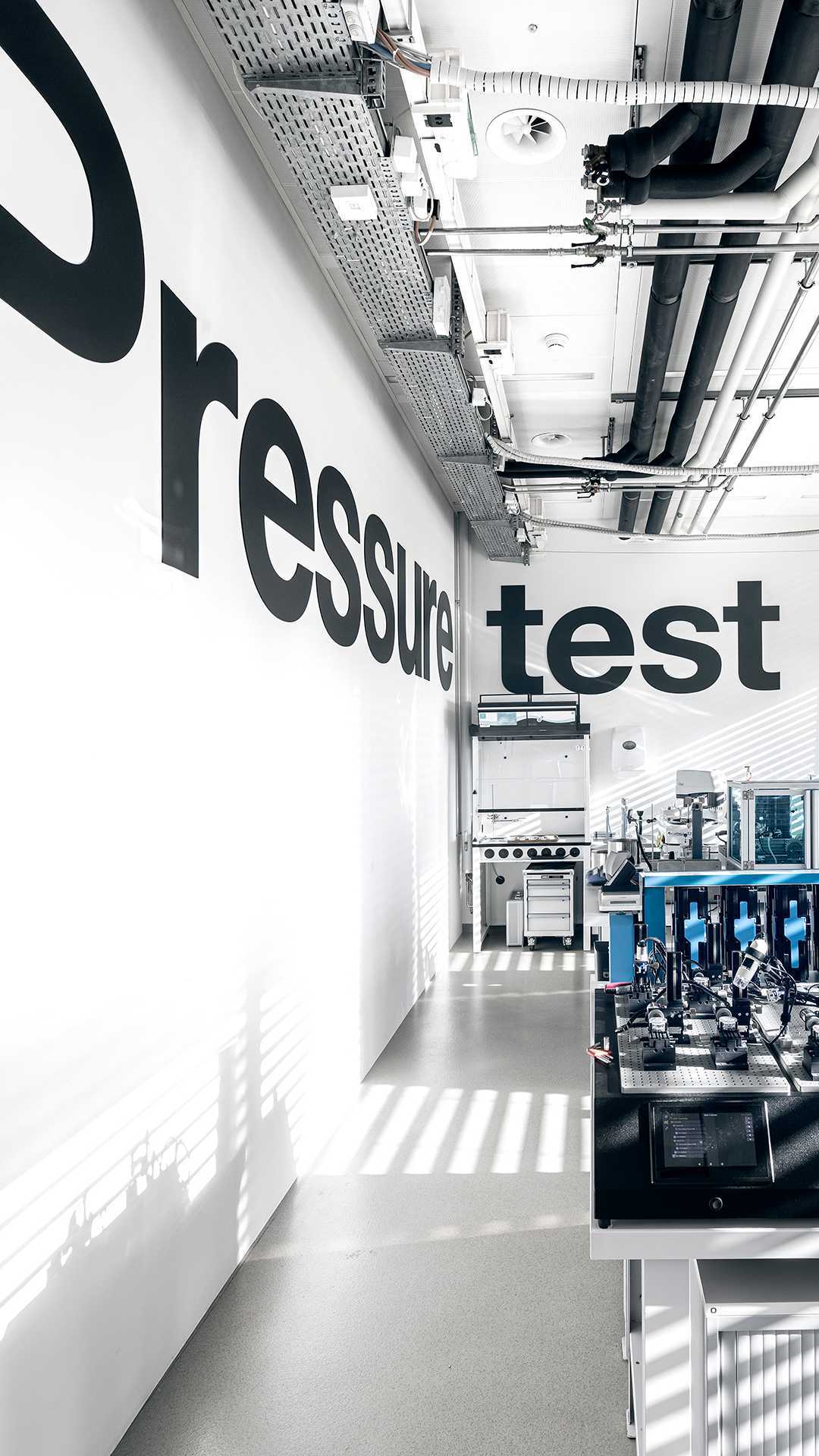
Mattia Aquila
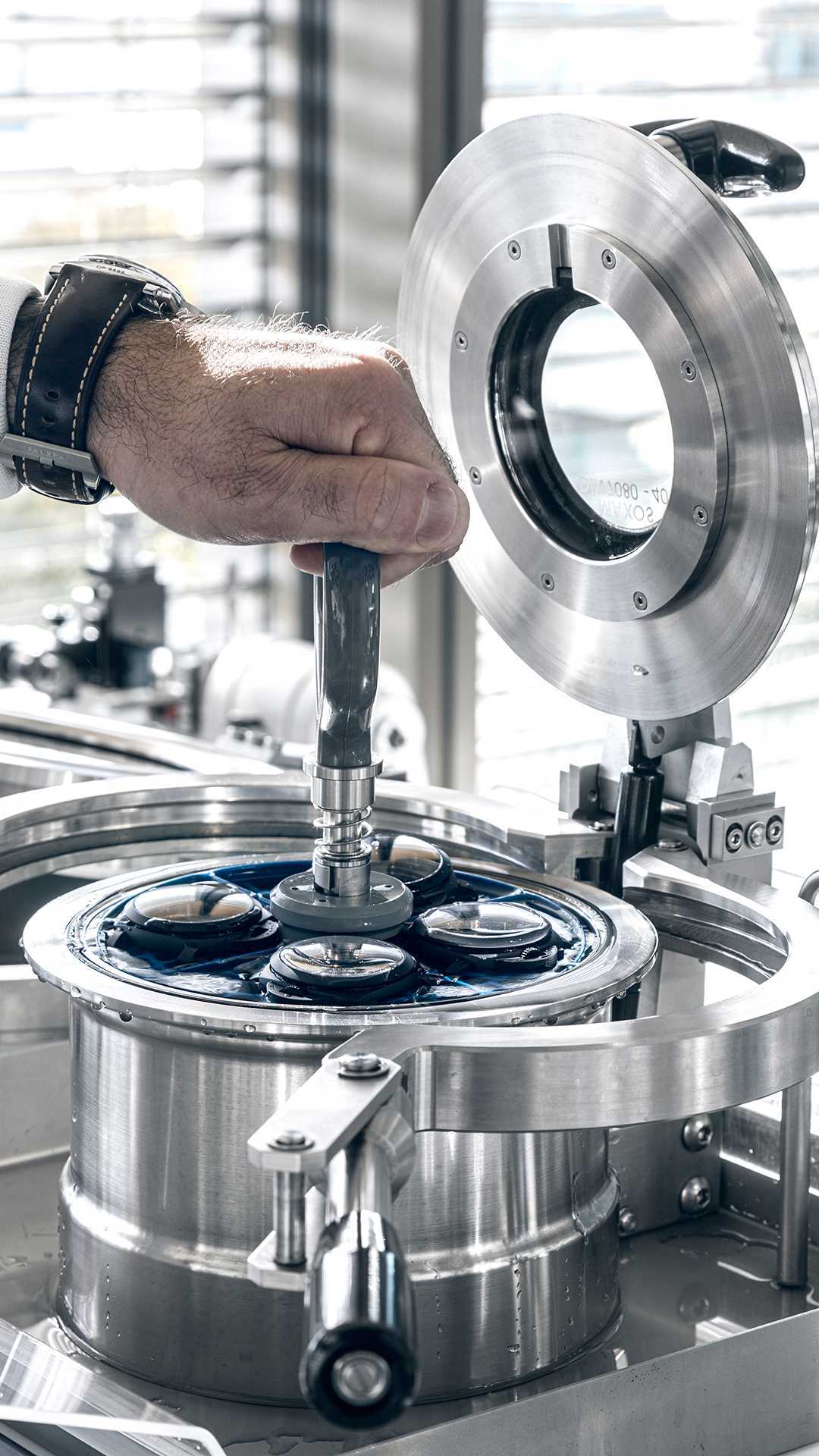
Mattia Aquila
One of my great fascinations with Panerai is the tension that exists between the past and the future – how historic designs provide the backdrop for some of the most groundbreaking material innovations you’ll find anywhere on the market in the pursuit of strength, robustness, and ultimately a dependable tool watch.
My walk around the manufacture with Mr Cavadini has, in a certain sense, told me nothing I didn’t already know about the brand: it makes some of the industry’s most hardy watches through meticulous testing and an obsessive compulsion for finding the next great material innovation.
In other words, if you’re mad enough to dive into Lake Neuchâtel on a winter’s morning, you might just have found the perfect watch to keep you company.
For more information, see panerai.com