The Vallée de Joux is the ticking heart of the Swiss watch industry. Home to the likes of Jaeger-LeCoultre, Patek Philippe, Breguet and Audemars Piguet, it is steeped in the history of world-renowned brands and game-changing timepieces. In other words, to venture into this narrow corridor of the Jura mountains – just one hour north of Geneva – is to journey back to the dawn of time itself.
The watch tradition in these parts owes its origin to the iron industry, whose presence in the region allowed for the manufacture of timepieces as far back as the early 18th century. Farmers were the first to adopt the craft here – who used the art to supplement their income during the leaner months – but as expertise was handed down, the art of horology grew in the villages dotted throughout the valley.
In Le Sentier, one of the largest communities, you will find the valley’s very first manufacturer, the maison of Jaeger-LeCoultre. Dating back to 1866, it is here that father and son watchmaking duo Antoine and Elie LeCoultre brought the area’s talented watchmakers under one roof for the first time, and in doing so transformed the Vallée de Joux into a global phenomenon.
The pair employed more than 500 watchmakers in house who set about creating in excess of 350 different calibres, from chronographs to minute repeaters. In the decades that followed, LeCoultre & Cie blank movements were placed at the heart of almost every big-name Swiss watch brand.
Nowadays, the Jaeger-LeCoultre manufacture encompasses a smattering of buildings, each built in a different era to accommodate the growing needs of the factory. It now stretches across 25,000sq m, employs 1,300 people, and creates close to 100,000 watches a year. If you ever wondered what it takes to put a Swiss watch on your wrist, it’s only when you step through JLC’s doors that it really starts to sink in…
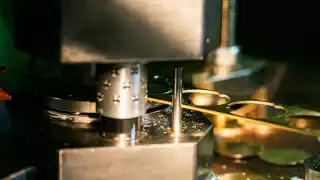
The production process begins at Decoupage – or cutting – where metals like brass, stainless steel and titanium are cut from bars to create the flat components of the movement
Johann-Sauty
Step One: Decoupage
Walking down the pristine halls of the manufacture, it becomes apparent that the creation of any watch requires an army of skilled craftsmen. The beauty of Jaeger-LeCoultre is not just in the hand-finishing of its timepieces or the exceptional movements inside the watch, but the fact that the brand takes care of every facet of the production process; even some of the largest names in horology cannot make this claim.
The beginning point is on the bottom level of the manufacture in decoupage. This is where metals like brass, stainless steel and titanium are cut from bars to create the flat components of the movement.
Each piece of the movement – the wheels, barrels, levers, cases and movement plates – requires a different suage (like a cookie cutter) that is added to the cutting machine to cut the intended shape. In the depths of the factory, there are some 6,000 suages on offer – ready to produce each and every intricate piece of a Jaeger-LeCoultre movement.
Huge cutting machines can exert up to 1.5 tonnes of pressure on the metal – a lot of force for even the tiniest of pieces. As we pass through, one craftsman is cutting the corrector for a moonphase (no bigger than a fingernail), while another creates the anchor for the iconic Jaeger-LeCoultre Atmos clock.
The birth of any watch cannot begin until the crucial pallets are glued to the lever of the escapement
Step Two: Assemblage des Ancres
The production process of a watch isn’t a linear pattern – there are often stages going on at the same time – but the birth of any watch cannot begin until the crucial pallets are glued to the lever of the escapement.
The pallets are the red synthetic sapphire ends located on each side of the lever. They make the escapement wheel rotate, and as a result make the balance wheel oscillate back and forth. To put it another way, the pallets are the component that create the tick-tock sound within the regulating organ of a watch.
Jaeger-LeCoultre was the first watch manufacture to make its own pallets. As more brands outsource this ancient art, JLC is also now one of the last.
Under a microscope, the pallet stones are glued to the levers with shellac – a natural resin secreted by the female lac bug (of course, you already knew that). Using a needle, only a fragment of shellac is required to keep the palette in place at the end of the lever but its placement needs to be precise. This step in the manufacturing process is crucial in the correct functioning of a finished watch and is still performed fully by hand at the manufacture.
The piece is barely the size of a long grain of rice, and yet is vital to the assembly process.
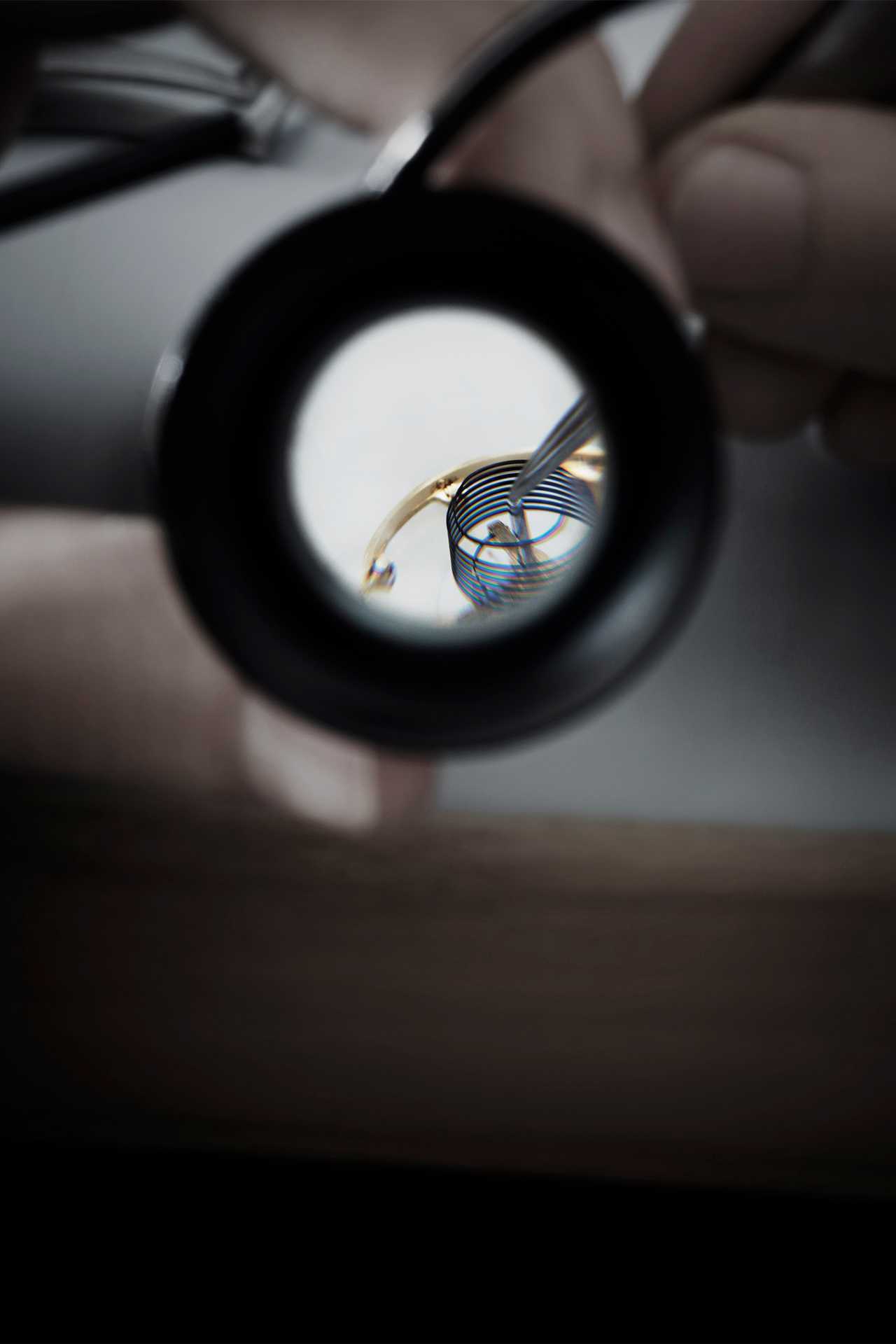
The balance spring is here being attached to the balance wheel – this is the part that creates the energy to power the watch
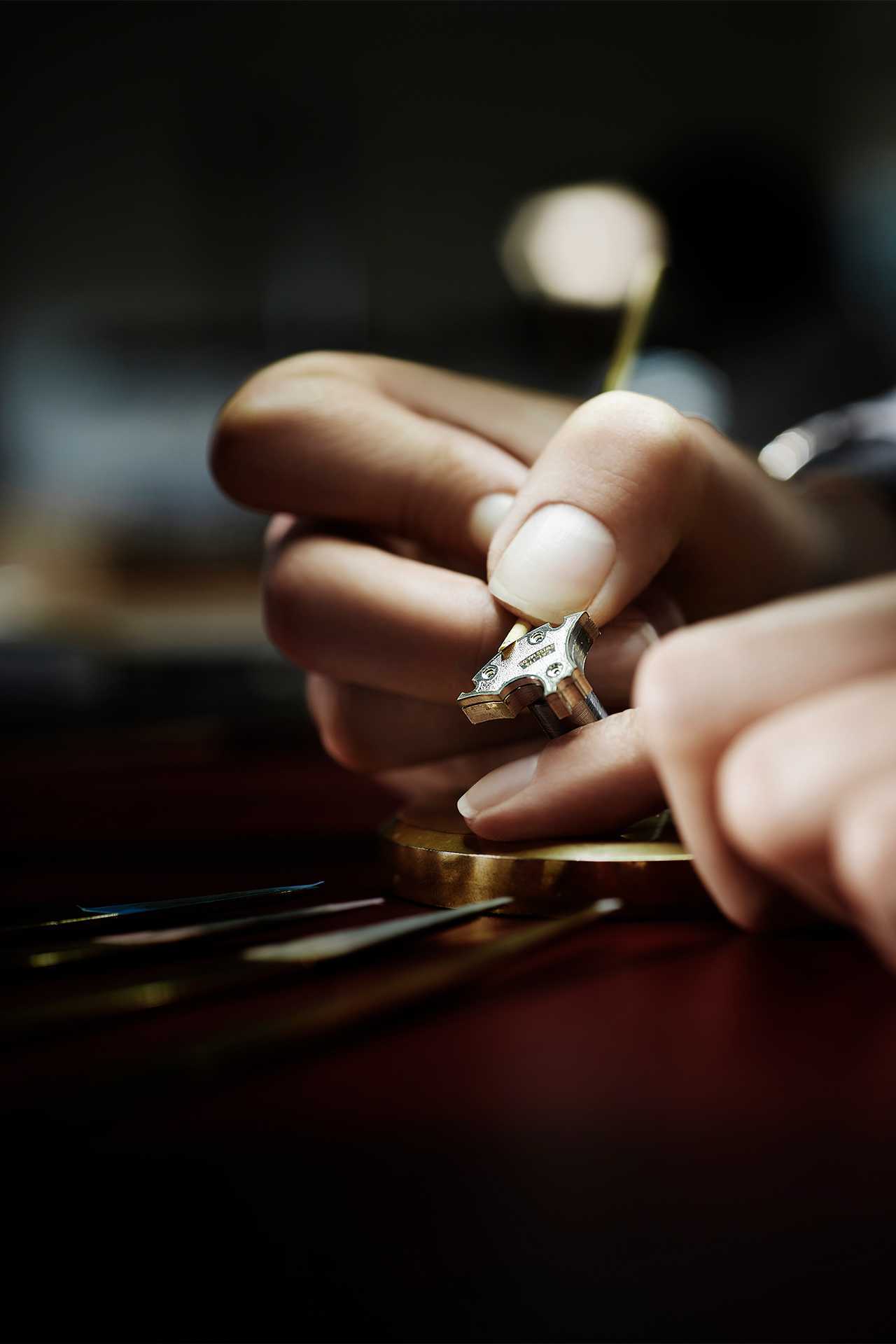
At JLC, each part of the movement is decorated for additional elegance – from perlage on the calibre to polishing each edge under a microscope
Step Three: The Balance Spring
Much like you’ll see in the world of shoemaking, for example, each small stage of the production process is the responsibility of as little as one person. At Jaeger-LeCoultre, every balance spring – the part of the balance wheel that creates the energy for it to oscillate – is looked after by Aline. Such is her specialism that were she to take a sick day or a vacation, production would stop until her return.
Her role is first to adjust the balance wheel to ensure the weight is perfectly, er, balanced all the way around. This is achieved by drilling small holes inside to make sure it is stable. Next, the balance spring is shaped manually from a single straight piece of metal. Each coil needs the same distance apart to ensure that the balance regulates the watch evenly as the coil unwinds during use. Such is the precision achieved that JLC watches on average are accurate to -0.5 to +0.5 seconds a day.
Step Four: Calibre Decoration & Assembly
Now the beating heart of the watch is ready, the movement begins to take shape.
The various components of the calibre are given an initial bout of decoration before being partially assembled. The decoration involved is known as perlage – a circular grain pattern, which is crafted by hand using a special spinning tool. Each of the different plates receives this treatment, while the chamfered edges on the bridge of the calibre are all polished under a microscope.
The devil is in the details, after all.
Each movement undergoes a whopping 1,000 hours of quality checks to maintain the brand’s high standards
Step Five: Jewelling
The jewelling workshop is not where diamonds and other stones are added to the dial, but instead where the rubies are placed on the bridge of the movement.
These jewels act as bearings in various parts of the calibre and are laboriously set on the plate or bridge with tweezers before being pressed in place. The rubies have two sides: one hollow and the other flat. The hollow side holds the oil so when the movement is running it lubricates it to reduce wear and tear on the components that are constantly moving.
Step Six: Movement Assembly
The final assembly of the movement is carried out by Jaeger-LeCoultre’s team of expert watchmakers. They carefully bring the various components together before each movement undergoes a whopping 1,000 hours of quality checks to ensure it maintains the brand’s customary high standards.
For the most complex pieces, the manufacture relies on its team of 45 master horologists, lead by head watchmaker Christian Laurent, who work in the Grand Complications department where pieces like the Westminster Perpetual Minute Repeater are painstakingly crafted.
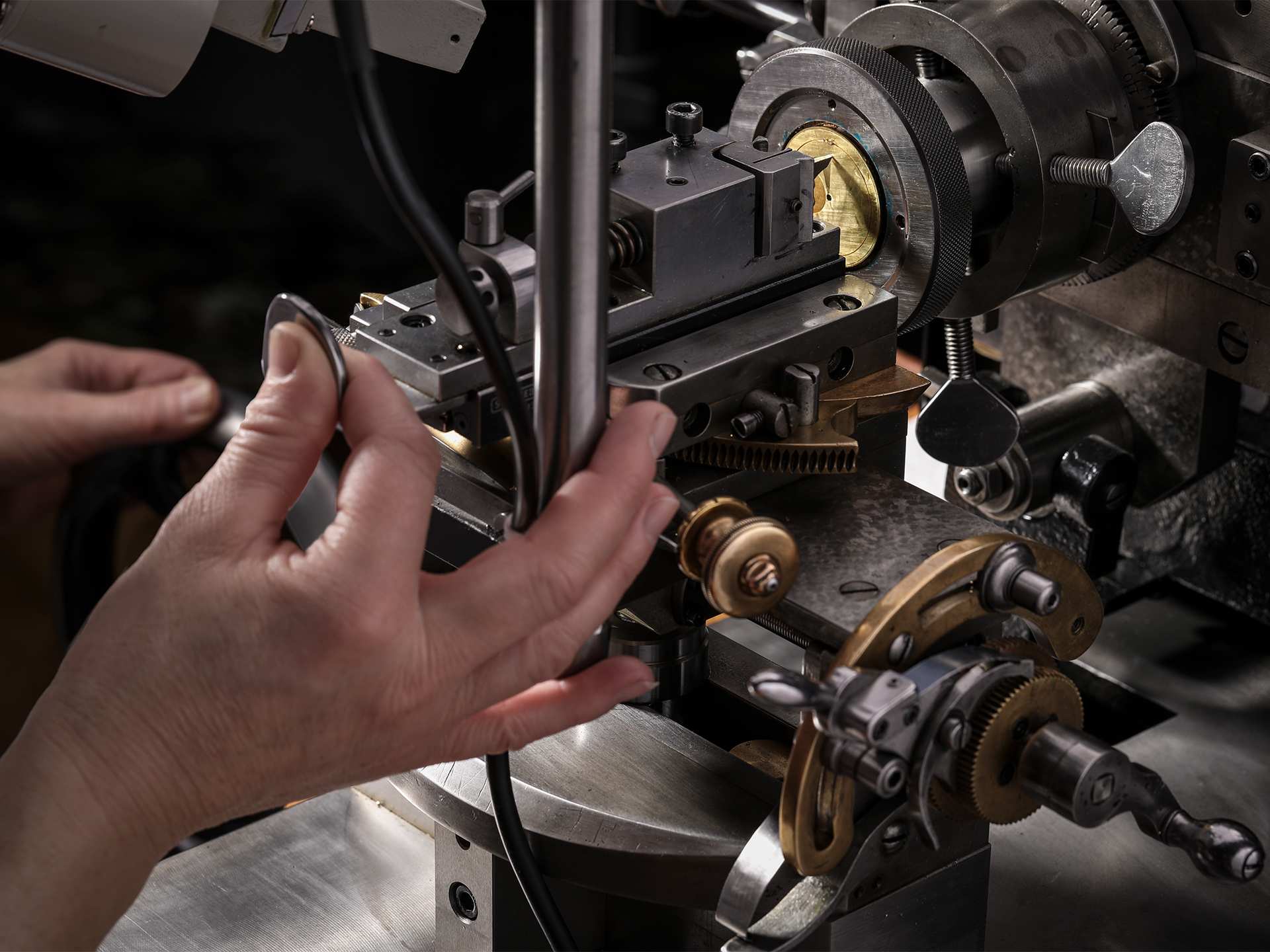
The delicate guilloché engraving is carried out using refurbished machines from the 19th century
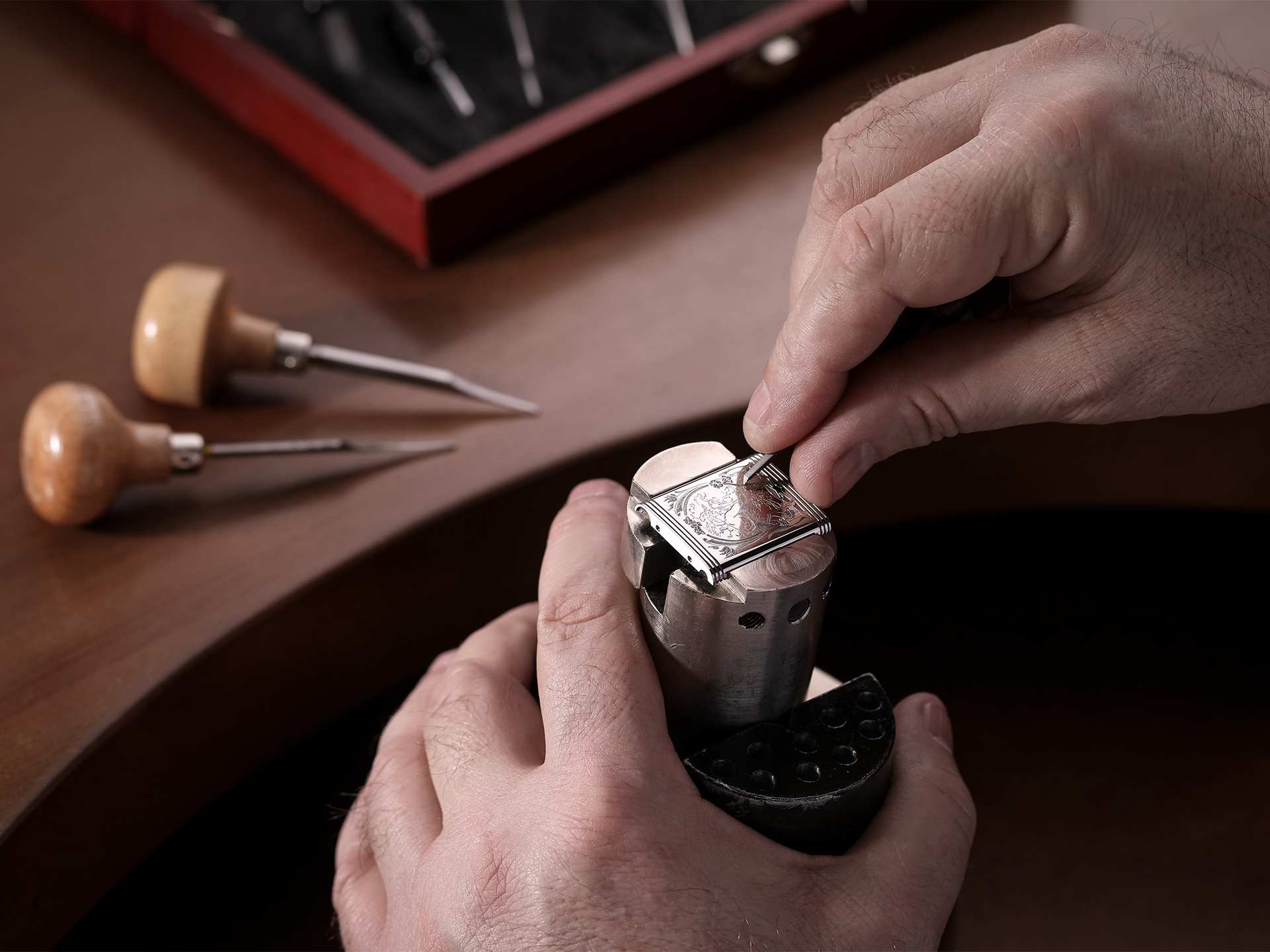
Atelier des Métier d’Art adds artistic flourish like the hand engraving on the cases of the Reverso
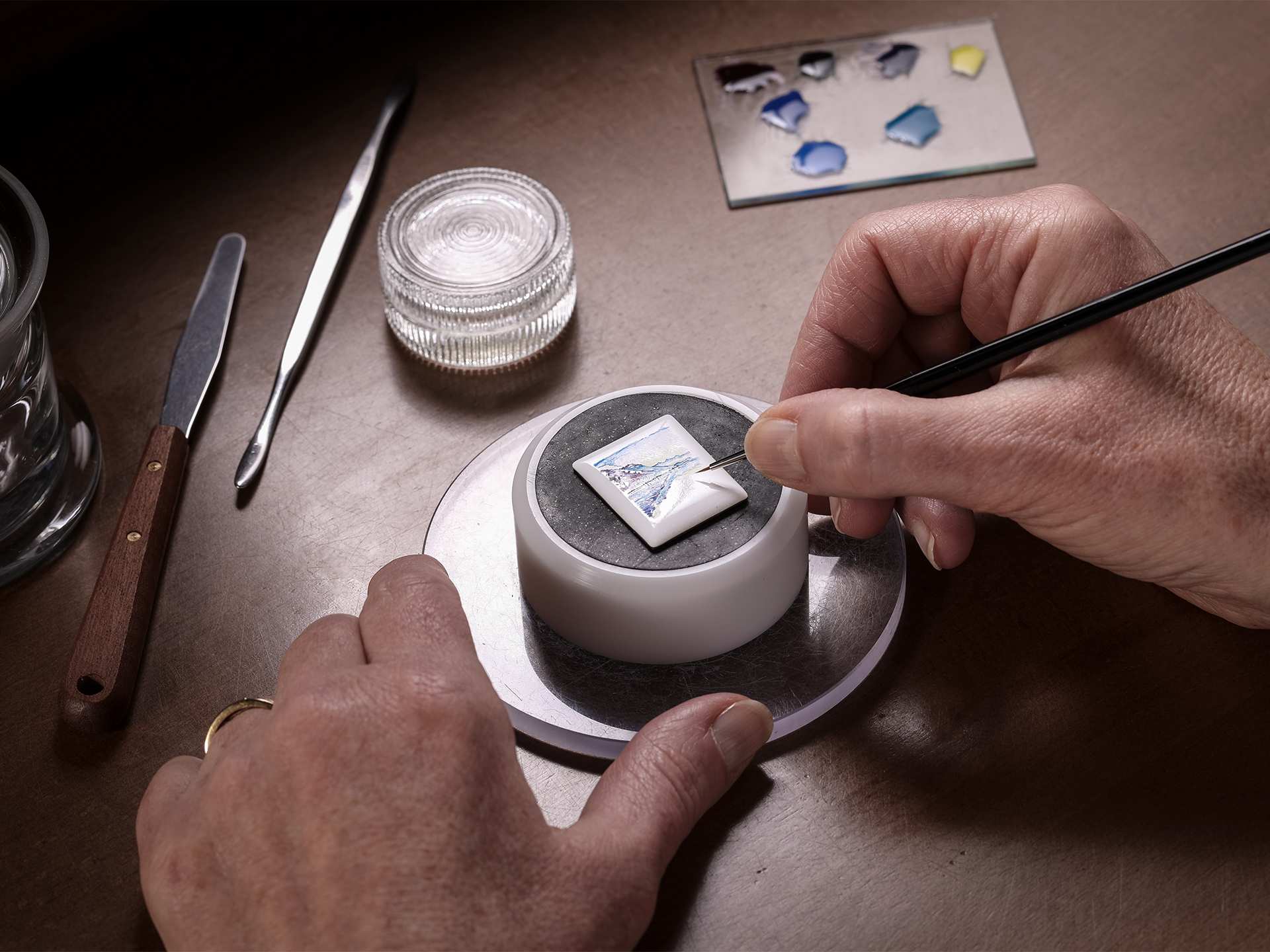
Time-intensive pieces like hand-painted enamel dials can take up to 100 hours to complete
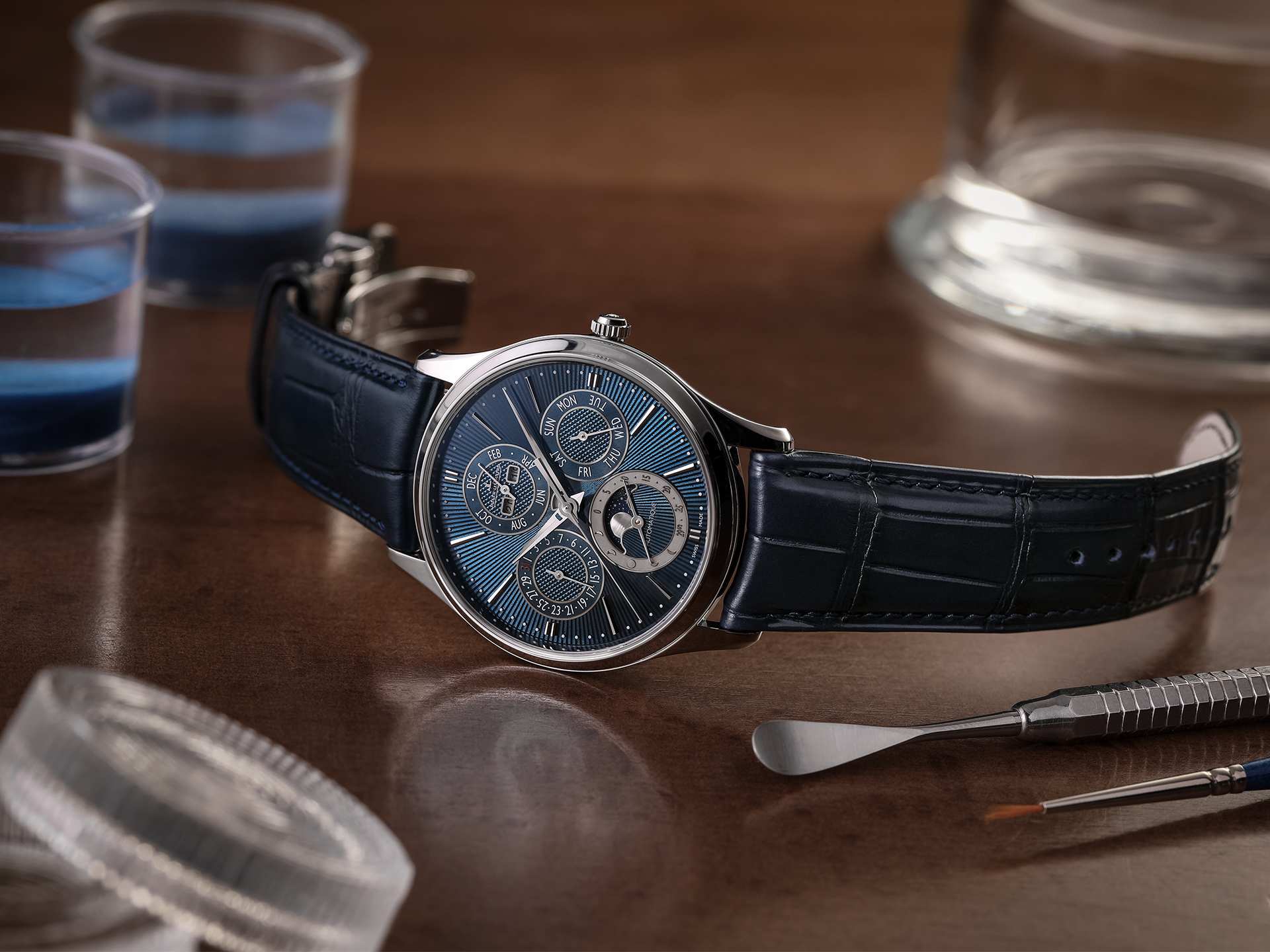
The finished product can look like the stunning Master Ultra Thin Perpetual Enamel – featuring a blue enamel dial and a vertical guilloché pattern
Step Seven: Atelier des Métier d’Art
It’s time for the finishing touches. The Atelier des Métier d’Art is the department that adds the artistic flourishes to a watch – whether that’s the hand-painted dials, the elegant hand engraving on the iconic Reverso cases or the setting of diamonds on the lady’s pieces.
This is some of the most time-intensive work that goes into the watch. The enamelling used to create some of JLC’s beautiful dials, for example, starts with around 30 different oxides, which are then blended to the desired colour much like a painter would with watercolours. Each layer is added to a metal disk, before they are fired in the oven at 800-1,200 degrees Celsius. The difficulty in constantly heating every new layer is the increased potential for something to go wrong – and that’s before you consider that the finished product has to be a uniform thickness with a flawless surface. Astonishingly, the most complex enamelling can take up to 100 hours to complete.
Elsewhere, intricate guilloché engraving is carried out using refurbished machines from the 19th century. Whether using the circular and vertical-lined guilloché pattern, each line needs to be meticulously drawn three times in order to create its elegant aesthetic.
Step Eight: Wear it
After the timepiece is completely assembled and passes quality control, there is nothing left the artisans can do but pass the watch onto its new owner. There’s a commonly held belief in the world of horology that buying a watch isn’t about the cost of the materials, but rather paying for the countless hours it takes to bring together this astonishing example of micromechanics and craftsmanship. However, until you’ve visited a factory for yourself, it’s difficult to imagine the scale of the operation required to create any one piece.
We don’t need watches to tell the time these days, but wearing a Jaeger-LeCoultre is to step back in history to an age where craftsmanship mattered above all. To us at least, that seems like time well spent.
For more information on Jaeger-LeCoultre’s history or to view the collection, see jaeger-lecoultre.com